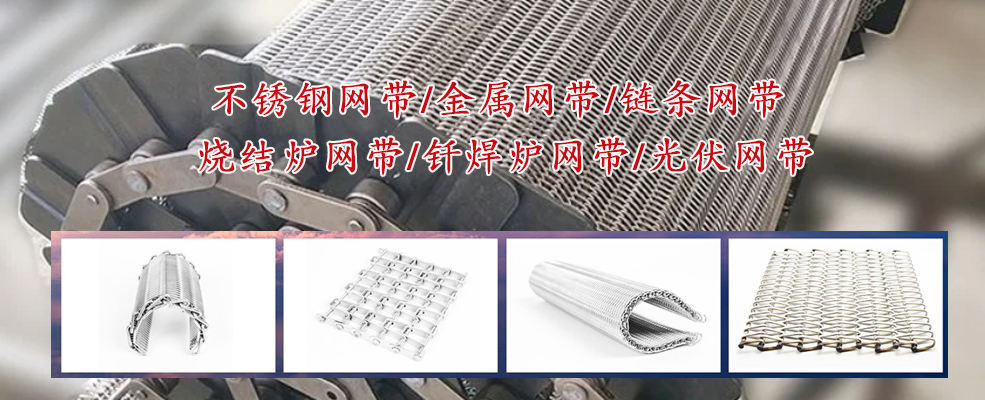
热处理与烧结作为现代工业制造中不可或缺的工艺步骤,广泛应用于冶金、汽车、航空航天等多个领域。而在这些工艺过程中,热处理烧结炉网带作为一种关键输送装置,其作用和地位不容小觑。网带不仅决定了工件在炉内的传输效率和效果,还直接影响最终产品的质量和生产成本。
热处理烧结炉网带在金属加工中的应用尤为广泛。对于钢铁等金属材料的淬火、回火、退火、烧结等热处理工艺,网带能在高温环境下保持稳定的输送能力,确保工件均匀受热。传统的网带多采用耐高温的合金材料制造,如不锈钢、镍铬合金等,这些材料具备极佳的抗氧化性和抗腐蚀性,能够在高温炉中长时间工作而不发生形变或断裂。网带的编织方式和结构设计也直接影响其性能表现。例如,细密编织的网带能够提供更好的支撑力和稳定性,适用于较小且精密的工件输送;而较为宽松的编织结构则适合大尺寸工件的传输。
在烧结工艺中,网带的作用同样至关重要。烧结过程通常在较高温度下进行,工件在网带上经过烧结炉时,必须保持均匀的温度分布和适当的通气性,以确保最终产品的致密度和力学性能。为此,先进的烧结炉网带不仅具备良好的热传导性能,还能够通过优化的网孔设计,提供最佳的气流通道,避免工件表面出现过烧或欠烧的现象。
除了传统材料外,随着科技的进步,新型复合材料的网带也逐渐进入市场。这些材料往往通过在传统金属材料中添加陶瓷、碳纤维等成分,显著提升了网带的耐磨性和高温稳定性。这些新型材料还具有更轻的质量,从而减少了设备的能耗,提高了生产效率。
智能化和自动化技术的发展也为网带的应用带来了新的机遇。现代烧结炉和热处理设备中,网带的运行状态和工件的传输轨迹可以通过先进的传感器和控制系统实时监测和调整,确保工艺过程的精准控制。这种智能网带系统不仅能提高生产的稳定性,还能显著减少人工操作的需求,降低操作人员的劳动强度。
热处理烧结炉网带在金属加工和烧结工艺中的作用不可替代。随着材料科学和自动化技术的进步,网带的性能和应用范围将进一步扩展,为工业生产带来更多的创新与可能性。在下一部分,我们将深入探讨网带在未来技术中的发展趋势,以及企业在选择和使用网带时应注意的关键因素。
在未来,随着工业制造向高效、环保和智能化方向的不断发展,热处理烧结炉网带的技术进步将主要集中在以下几个方面。
首先是材料科学的突破。当前,传统金属材料虽然在耐高温、抗腐蚀方面表现优异,但在一些极端工况下,仍然存在使用寿命有限的问题。未来,研究人员将致力于开发更加耐用的新型合金材料以及高性能的复合材料。例如,通过在不锈钢基础上添加稀土元素,能够显著提升材料的抗氧化性和热稳定性;而陶瓷基复合材料则可能在极高温环境下表现出超越金属材料的卓越性能。这些新材料的应用,将使网带在更苛刻的工作条件下仍能保持高效稳定的性能,从而降低设备的维护成本和停机时间。
先进制造技术的应用也是未来网带技术发展的重要方向。3D打印技术在制造复杂结构网带方面的潜力巨大,通过3D打印可以实现传统工艺难以制造的复杂几何形状,如具有特殊孔径和流体通道的网带。这不仅有助于提高网带的通气性和热传导效率,还可以根据特定工艺需求定制独特的网带结构。表面处理技术的进步,如等离子喷涂、物理气相沉积(PVD)等,也将在网带的耐磨性和抗腐蚀性能方面发挥重要作用。
在智能化方面,随着工业4.0和物联网技术的广泛应用,热处理烧结炉网带将进一步与智能监控系统相结合。通过集成传感器技术,网带的运行状态,如温度、张力、磨损程度等,可以实时传输至中央控制系统进行分析和调整。这种智能监控不仅能够及时发现并预防潜在故障,还可以通过大数据分析优化生产工艺,提高生产线的整体效率。智能化网带系统还可以实现自我诊断和远程维护,进一步降低企业的运营成本。
环保方面,未来的热处理烧结炉网带将更加注重节能降耗和环境友好型设计。通过使用轻质高强度材料,不仅能够减少网带的自重,降低传输能耗,还可以提高热处理设备的整体能效。研发环保涂层和材料,使网带在生产过程中减少有害气体的释放,并能够在更高的温度下运行,进一步提高能源利用效率。这些技术进步,将帮助企业在实现可持续发展的满足日益严格的环保法规要求。
在选择和使用热处理烧结炉网带时,企业应充分考虑工艺需求、材料特性和设备性能等多方面因素。不同的工艺环境对网带的要求不同,企业应根据具体的应用场景选择合适的网带材料和结构。定期的维护和检查也是确保网带长期稳定运行的关键,通过对网带的磨损情况、张力状态等进行监测,可以及时发现问题并进行处理,避免因网带故障导致的生产中断。
热处理烧结炉网带的技术进展正在不断推动工业制造的升级与转型。随着新材料、新技术的应用,网带将展现出更强的性能和更广泛的应用前景。企业在关注技术发展的也应积极探索如何在实际生产中更好地利用这些新技术,以提高生产效率、降低成本,赢得市场竞争优势。